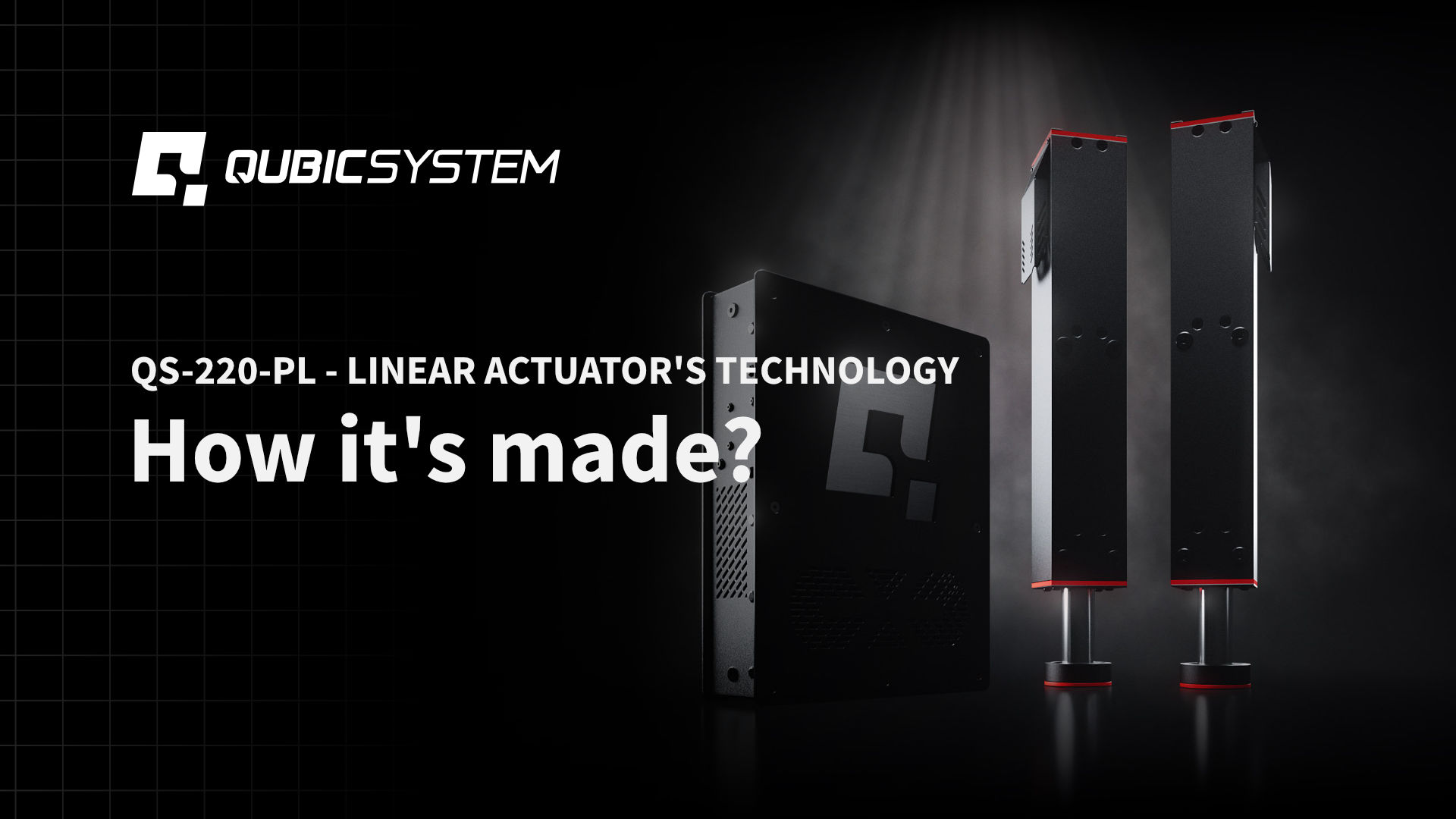
Why we decided to develop our own linear actuator and how it’s made?
The world of simulation and home simulators has reported a significant increase in popularity during the past couple of years – especially due to the coronavirus pandemic, which has blocked access to real events. Along with the growing simulation market, the concept of transferring motion solutions from professional systems for personal use. However, the difference in the expectations and requirements of home users has posed new challenges for the motion platforms engineers.
In professional motion simulators, a high payload and a wide range of motion are necessary, also the dynamics and precision of the entire motion system are not without significance.
On the other hand, in the sim racing world, where the philosophy of “less is more” reigns, the parameters such as immersion, work culture and modularity are the key. From the hardware side, this translates to high dynamics, smooth movements in the full speed range, the possibility of creating systems with various degrees of freedom and extremely important for home users, the low noise emission.
Over the past few years, engineers at Motion Systems have analyzed and mechanically tested many of the linear actuators. During months of testing, they have encountered certain limitations related to performance, lack of precision, smoothness of movement, service life (especially during vibration) and excessive noise in the various popular products. We saw that there was no room for compromise and took the decision to develop our own linear actuator.
Throughout the evolution process, we had many different concepts for the perfect linear actuator, the most promising ones were tested in reality by building and testing prototypes (destroying most of them along the way). During this process lots of mistakes were made, but the effort was not in vain. Now we can present and explain why we are so proud of the only such linear actuator in the world, which took us more than 4 years to develop.
Our project’s basis was to develop linear actuator technology that would be part of a wider ecosystem and meet the range of requirements of both the professional and domestic user. In short, we wanted to do a technology transfer from larger motion systems to home solutions.
We achieved this by focusing on the design of the actuator. In addition, the appropriate selection of the components of the mechanical design so that they are able to carry out the desired movement through our proprietary electronics and software.
So let’s take a closer look at Qubic System linear actuators
The QS-220-PL motion system is a response to the market demand for plug and play solutions. The external appearance is based on geometric versatility, and the cubic shape allows it to be adapted to most popular cockpits available on the market. QS-220-PL was created as a two-actuated system that can be configured into motion systems with 2-6 degrees of freedom.
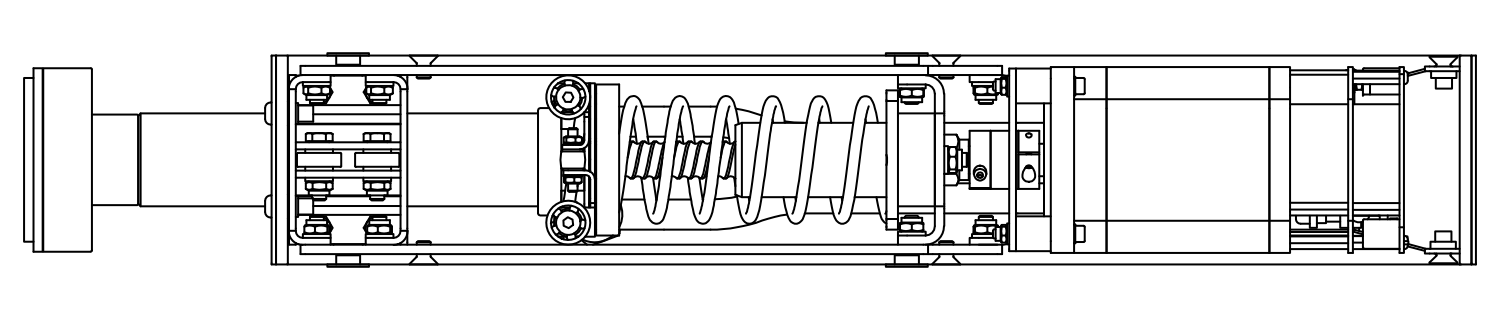
MOTOR AND DRIVETRAIN
Currently, the drives that offer the best dynamic parameters and power density are synchronous motors with permanent magnets (PMSM). They ensure full torque control in the entire rotational speed range as well as small moments of inertia of the motor and high overload, which translates directly into the possibility of achieving high accelerations of the entire system. On the other hand, commonly available systems for transferring rotary motion to translational motion with the highest efficiency are the combination of a ball screw with a nut, which ensures smooth movement and high positioning precision. The combination of these elements and a dedicated control system ensures smooth and dynamic operation of the QS-220-PL motion platform.
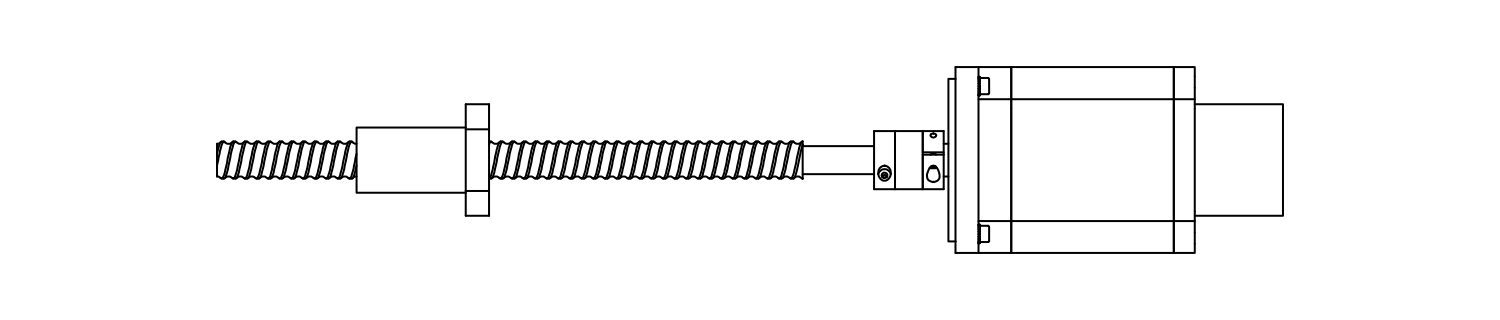
PISTON ROD GUIDE
Standard actuator piston rod guide systems are designed on the basis of slip rings made of plastic, cast iron or non-ferrous metals. This ensures high structural rigidity and relatively quiet operation. However, the sliding connection is also subject to a number of effects:
- stick-slip friction phenomenon
- wear of guide rings
- heating of the piston rod
In professional motion solutions, these problems are solved by continuously lubricating the system with oils containing the appropriate additives and by adding compounds such as molybdenum disulphide MoS2 or graphite C to the guide rings. The high rigidity of the system makes it possible to safely reach extreme device positions that cause extremely uneven loads to be generated on the individual cylinders (example PS-6TL-1500 motion platform).
As oil lubrication of the system is difficult in domestic solutions and the envelope of the machine’s movement is incomparably smaller, an alternative guiding mechanism was developed which, instead of attempting to minimize the friction phenomenon, makes the most of it by transferring it to the rotary movement. This completely eliminates the stick-slip phenomenon, the heating of the piston rod and is also characterized by extremely low noise emissions.
The system provides a lower connection stiffness, but with the low-tonnage solutions for which the Qubic System motion platforms were developed (below 500 kg), this does not adversely affect the stiffness of the overall system. The quality and performance of this solution has been tested, proven, confirmed and patented.
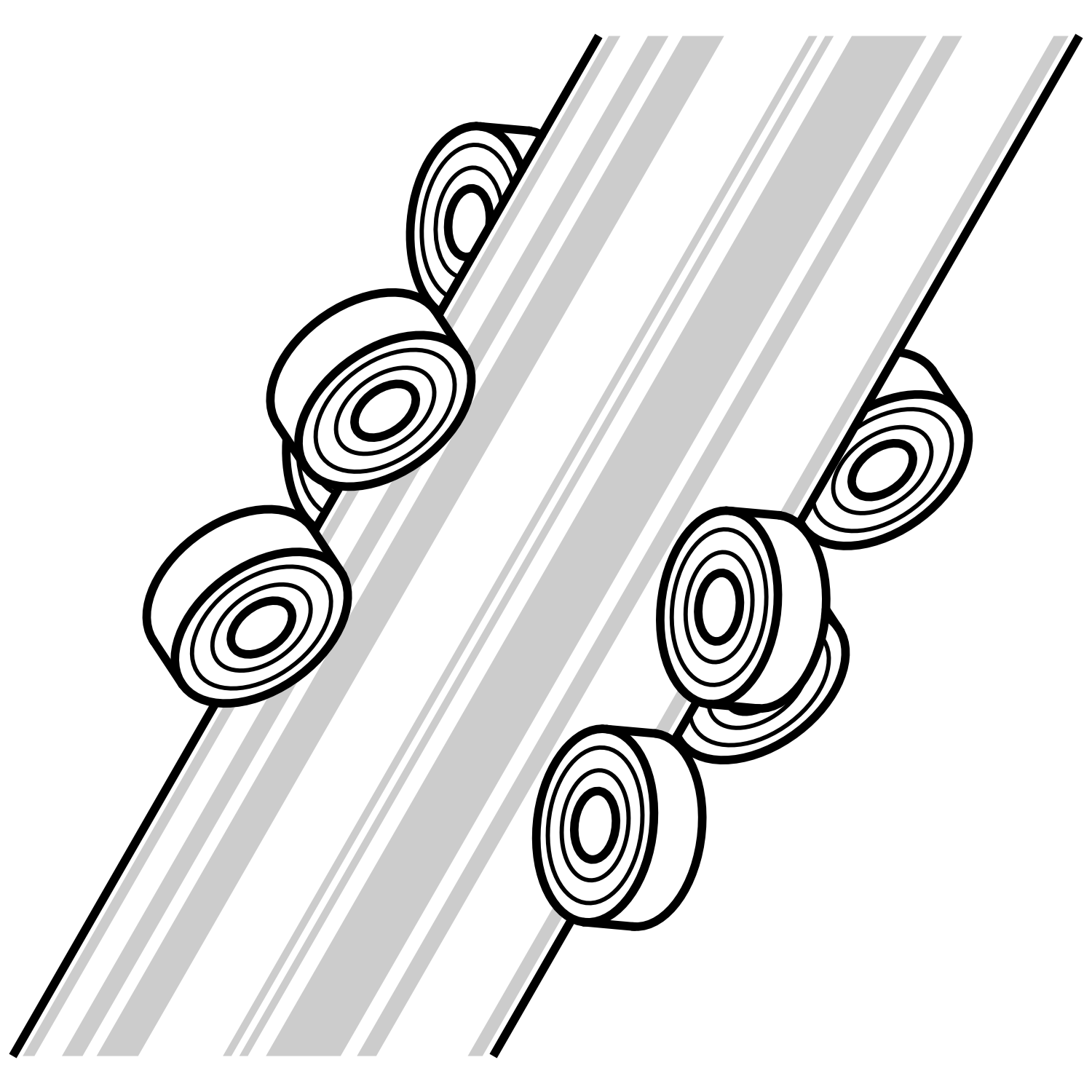
GRAVITY COMPENSATION
This mechanical design of the actuator, with its ultra-low coefficient of friction, translates into its dynamic and performance, very low noise emissions and smooth movement, which in turn enables the transmission of vibrations up to 100 Hz (haptic feedback).
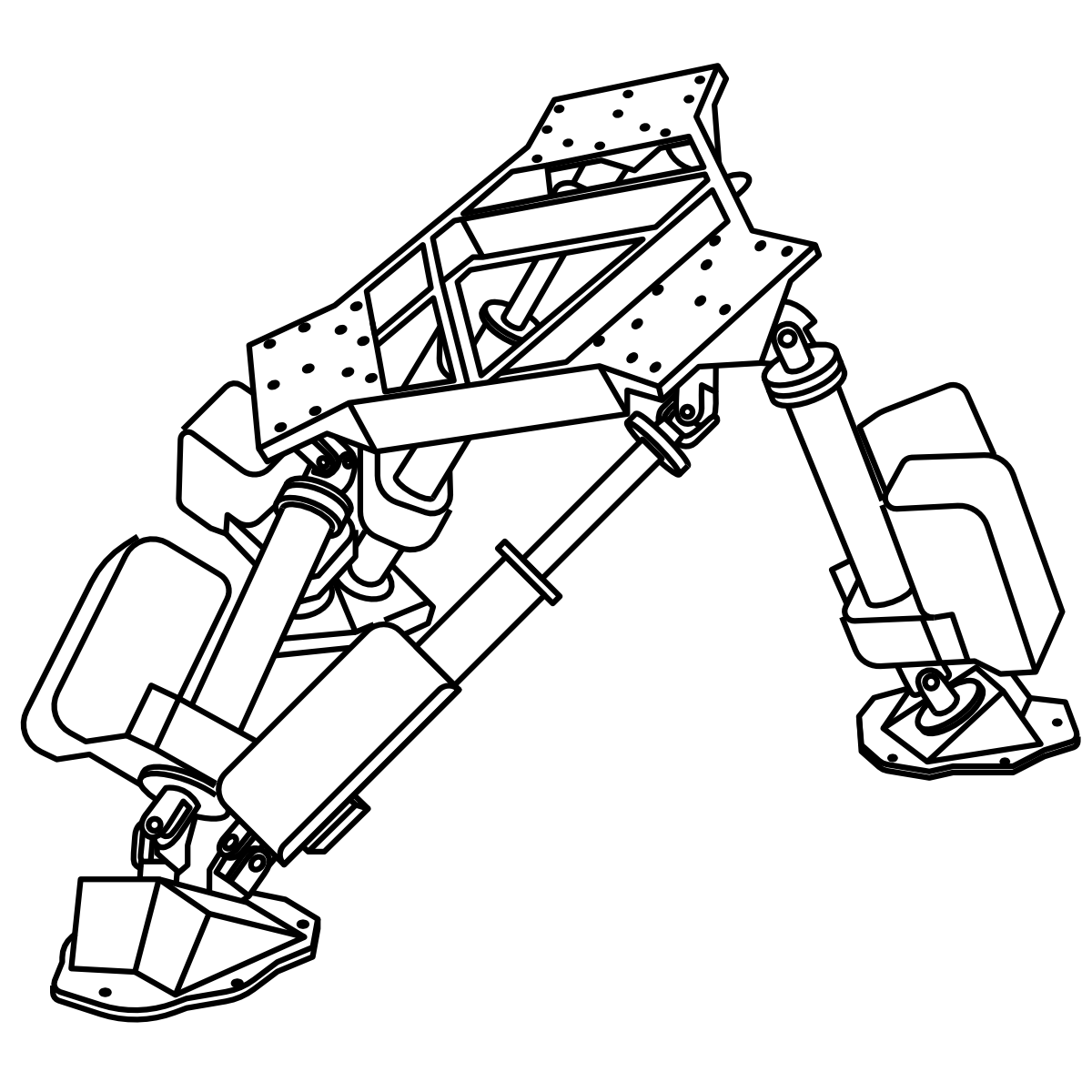
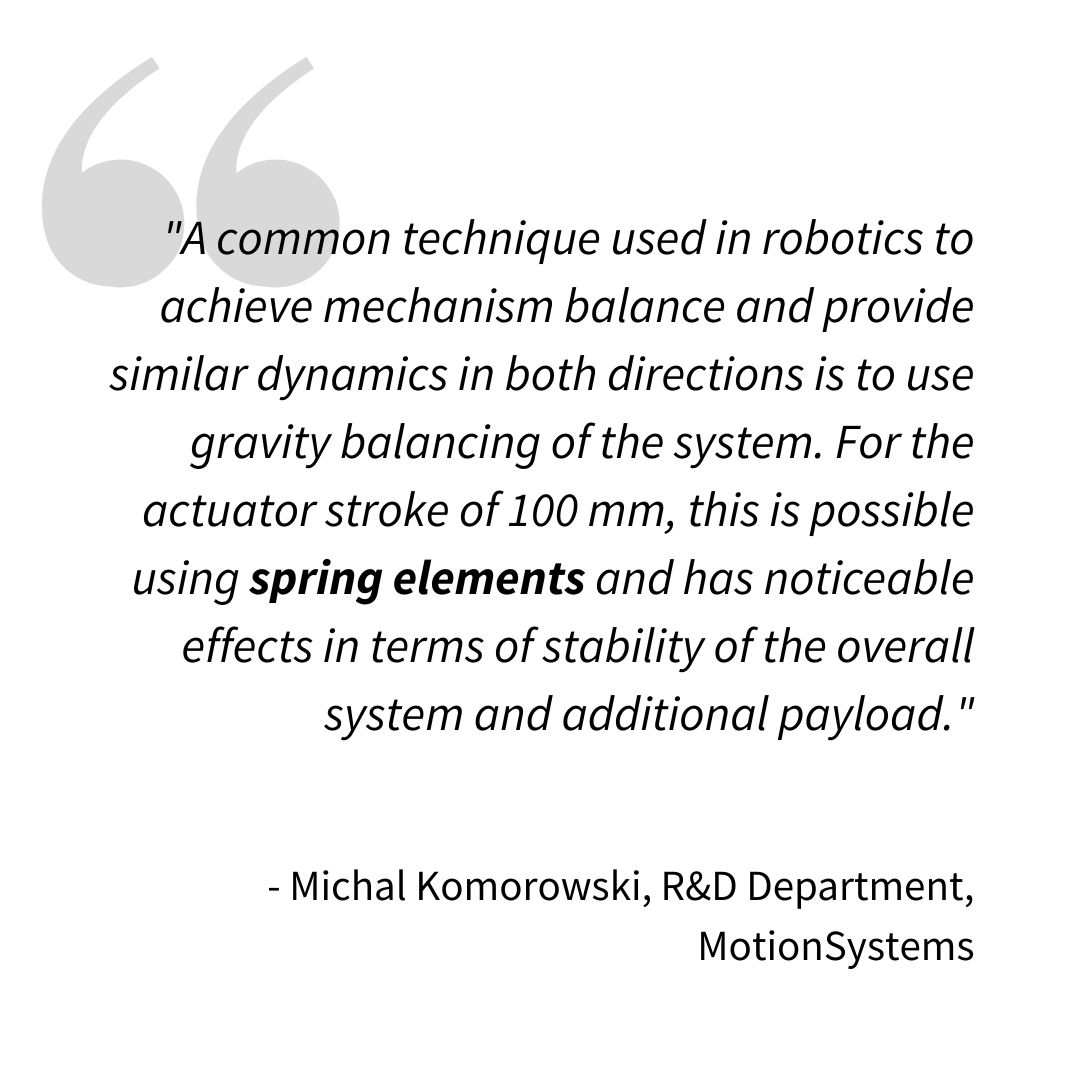
ADDITIONAL EFFECTS – HAPTIC FEEDBACK
The most common additional cockpit systems used to increase immersion are:
- platform motion systems
- seatmovers
- buzzers based on haptics systems
Tests have shown that motion systems with very high dynamics are able to replace vibration devices – buttkickers – as their supplementary function. The symmetrical arrangement of the actuators in relation to the operator ensures sufficient vibration coverage of all segments of the workspace. However, the best effect can only be achieved if the specific amplitude-frequency components are properly isolated. In the case of the QS-220-PL system, this has been reached through the use of a dedicated motor flange and coupler with a suitable damping factor.
Full control of the ecosystem from both the mechanical, electronic and software sides gives you the opportunity to choose the motion system that will suit your simulator. What’s more the system guarantees that you can start your adventure with motion systems from a set of 2 actuators to have the option to expand with additional sets in the future. We are pleased to announce that further solutions will be added to the Qubic System family.
After these years of development, we can confidently say that our design goals have been achieved and crowned with a patent.
In the next part of our educational articles, we will take a look at the Qubic System from the electronics side. Enjoy!